Prioritize maintenance tasks and optimize your strategy with asset criticality analysis
Are you seeking more control over which assets are most important to your organization and a better way to plan? The Asset Criticality Analysis gives detailed insights into assets that are crucial to your operations. This lets you prioritize the most critical maintenance tasks, prevent unnecessary failures, and ensure more efficient planning.
The new assessment functionality provides a practical approach to assessing assets based on various aspects and effects. This enables you to:
Choose the right maintenance approach for each asset.
Save time and costs by focusing maintenance on the most critical assets.
Prioritize the maintenance tasks that impact your business continuity most effectively.
There are two different methods for using an assessment. A method to calculate the criticality with only a Probability (MTBF) or a method where the Duration (MTTR) is also considered. This last one can indicate whether there is an impact on production planning.
The MTBF and MTTR are calculated automatically based on Ultimo's asset information to simplify, reduce setup time, and eliminate manual data lookup.
Asset criticality on objects
A new tab called 'Criticality' is added to asset and process function screens, giving information about the last criticality assessment. It also provides a grid with an overview of the history of criticality assessments for this equipment.
Additional information
The new module is available in Premium (optional) and Enterprise. The criticality assessment applies to the following assets.
Technical Service: Equipment, Inventory and Process functions
Infra: Objects and Elements
IT: Configurations and Configuration-Items
Fleet: Objects and Fleet Numbers
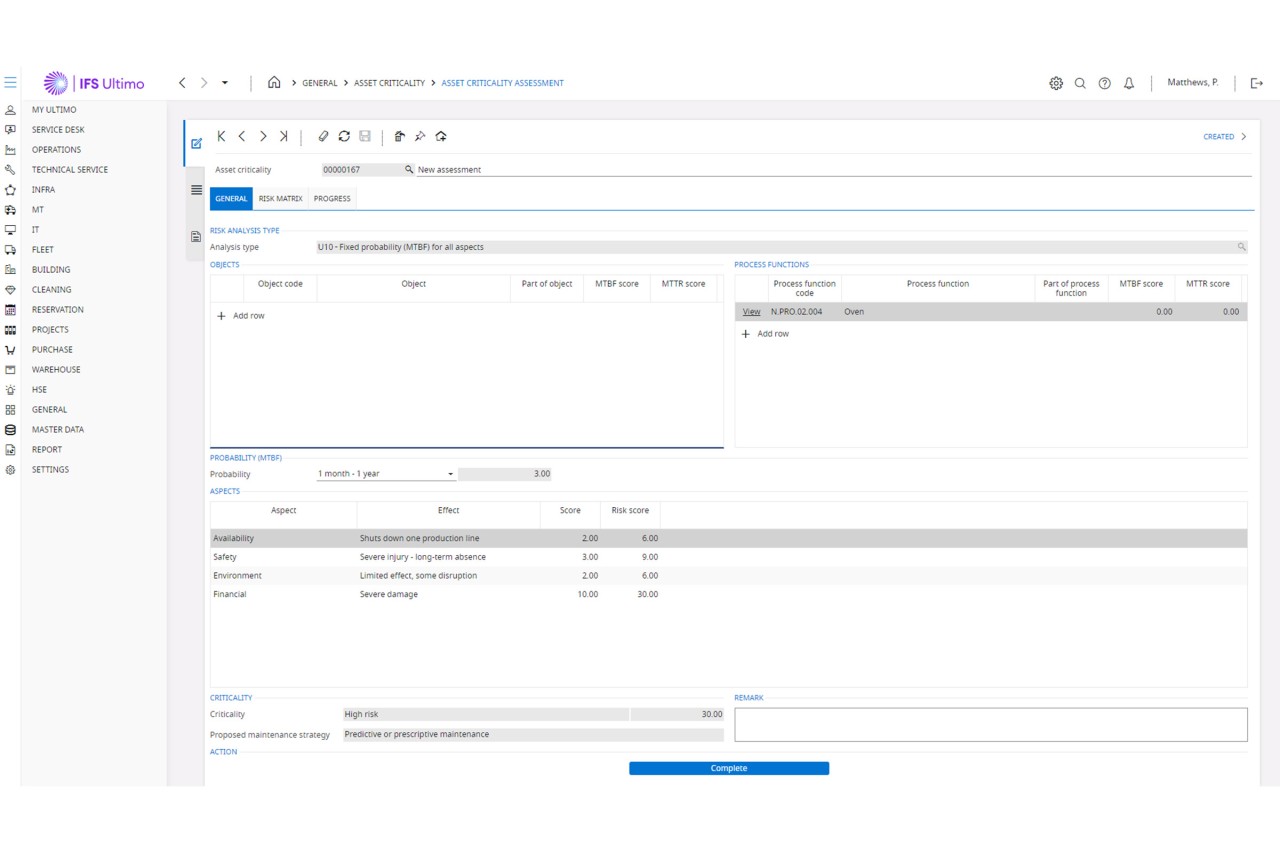
Enhancing reliability with structured failure data & analysis
According to the Pareto principle, 80% of the outcomes result from 20% of the causes. By identifying why assets are failing, a large part of the failures can be prevented in the future. Efficient failure analysis starts with structured data. Adding structured fields for the Failed Component, the Component Problem and the Remedy next to the already existing field for Failure Cause, enables a more detailed failure analysis.
Our new BI report for Failure Analysis highlights bad actors, cost drivers, and performance killers. It provides insights into your worst-performing assets, key failure drivers, and related costs. This helps you to make data-driven decisions to improve your maintenance strategy and prevent recurring failures.
Root causes of failures with effective RCA
Pinpointing the true cause of failures is essential for enhancing asset reliability and preventing future issues. This functionality uncovers the underlying reasons behind failures. You can use the 5 Why method and implement follow-up actions to ensure thorough resolution and long-term reliability improvements.
Key features include:
Performing a structured RCA with the 5 why method
Initiating an RCA directly from a job or HSE-incident
Gaining deeper insights in the historical context by recording related timeline events
Creating follow-up actions (Moc’s, Jobs, Actions) to prevent recurring issues
Managing the RCA team with optional sign-off