Sorry, we couldn't find any results.
2400+ customers trust IFS Ultimo
2400+ customers in different industries trust IFS Ultimo to optimize their frontline VIPs’ satisfaction and the performance of over 15 million assets worldwide. Who better to tell you what IFS Ultimo’s EAM does for our customers than our customers themselves?
Trusted for ease & value
Preferred by uptime champions and goal-crushing operational leaders worldwide
Working smarter with Ultimo Premium saves us at least 1 FTE in time, because all asset data are recorded, and we no longer have to search for missing maintenance and service or quality data.”
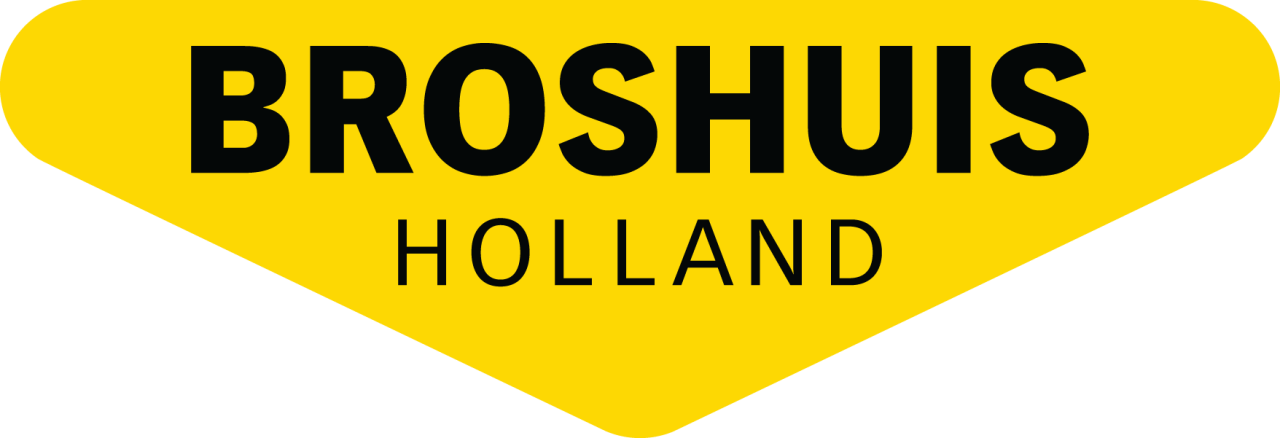
Even with just the improvements in purchasing alone, we are already looking at an annual savings potential of 5% of our purchasing volume.”
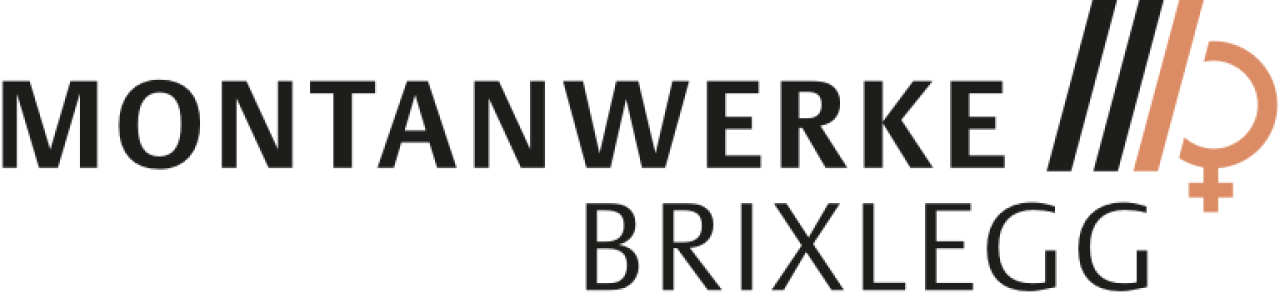
The FMECA strategy in Ultimo has helped us reduce the downtime by 40% and realize considerable cost savings.”
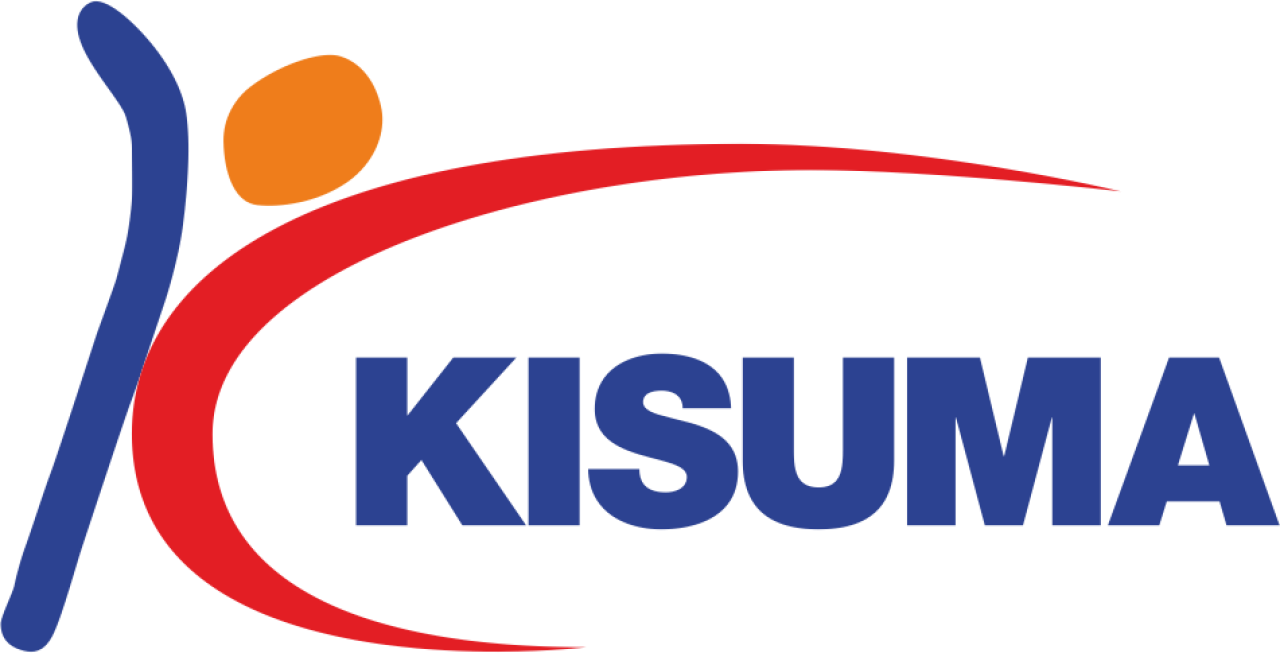
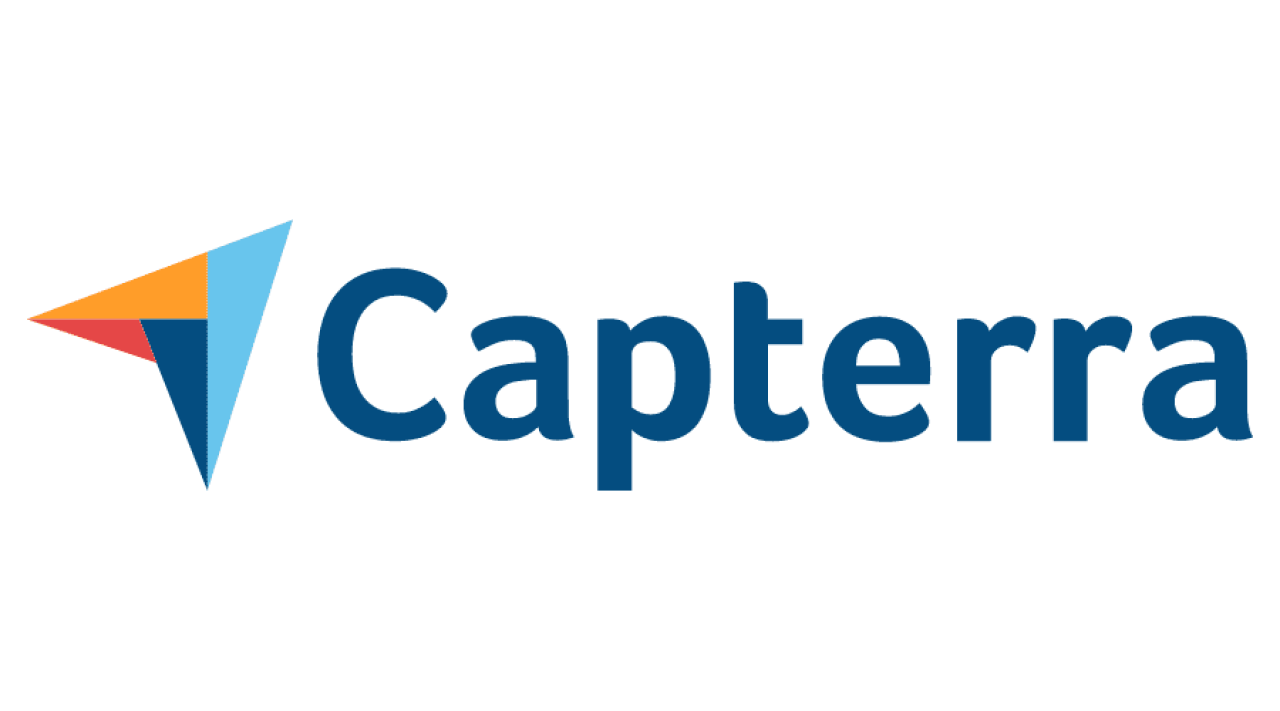
The flexible configuration options of the software make it possible to adapt it to your own processes. That makes it very user-friendly.
We were able to realize a Return on Investment in Ultimo within two years.”

We earned back the total costs of implementing Ultimo within six months”
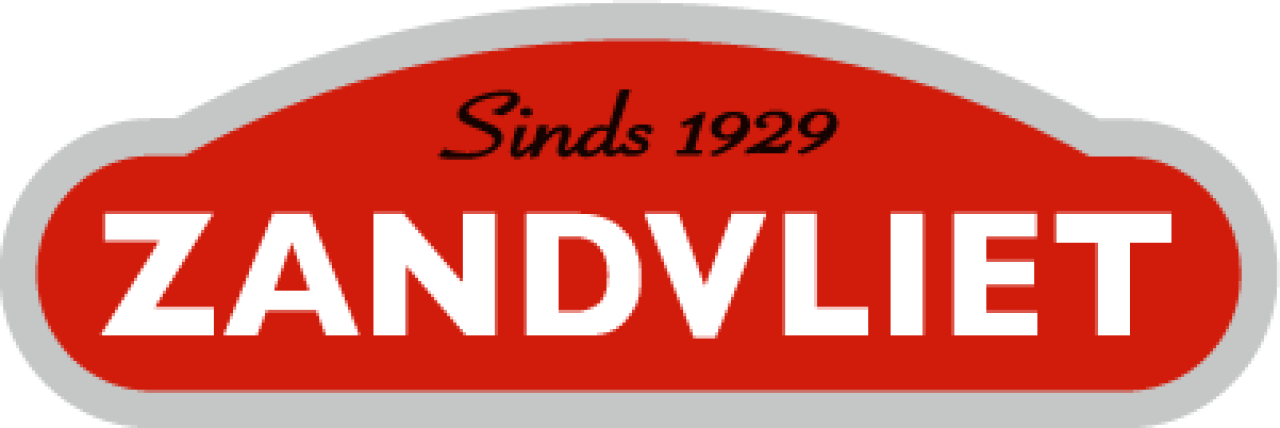